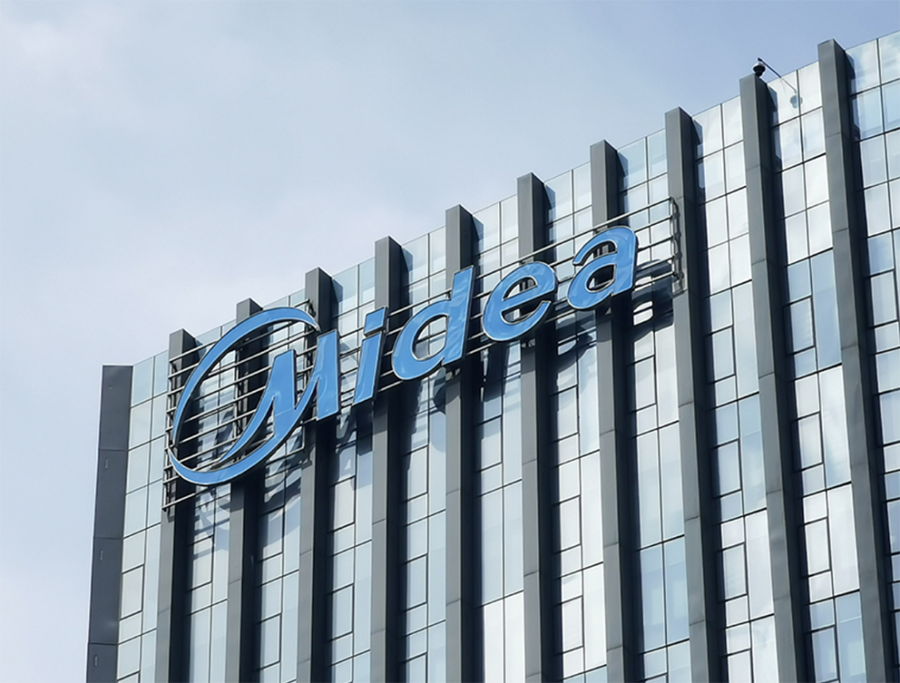
▲ 美的集團
從精實生產踏上了智慧製造之路
2014年3月5號是我第一次見到詹老師,聽到詹老師的課。當時美的集團的戰略是「產品領先、全球經營、效率驅動」,而在效率這個方面,是當時制約美的集團發展的短板。美的集團的績效從集團往事業部,再層層分解至部門、模組、最後落到每一個人頭上。而集團的要求是,每年各項指標都必須要有提升的,若是沒有能力去改善績效,根本無法在集團內立足。當年美的集團有30多個工廠,工廠本身水平參差不齊,為了使各工廠統一系統性去開展精實生產,集團抽調了七個事業部各個工廠的核心人員,參與詹老師的精實生產課程,而我正好是抽調名單中的一員。
當年4月,老師本是來順德輔導研發,但也抽了空去了各個廠,想看看上過課以後,精實在廠內推行得如何。當時在中國沒有拉動這個概念,美的集團各廠又產品型號繁多,在各廠人員受TPS影響較深時,用超市拉動難以成功,讓老師有點失望。因為我們壓縮機廠的工藝流程較長,關鍵零部件又全是自製,老師在親訪我們壓縮機廠之前,本認為我們會是最難成功拉動的。
在同年5月3號,老師親自來我們現場,拿著我們容器上的看板,看完成時間與後面總裝真正的使用時間,發現這兩個時間差控制得還可以,基本上能保證今天做出來的零件在明天下午之前用掉,是有一定的拉動的邏輯在的,這才在課堂上建議大家來我們廠觀摩,讓我之後忙了兩個月,接待了20多批次的同事們。之後甚至成立了「拉動組」,將拉動的方法在美的集團的各廠推廣。
我們自2005年就有使用看板,但當時只有兩個概念,一是零件不要比總裝早太多完成,二是總裝前9個自製零件都要做好,對於庫存的設計和前製程各個零部件應該開始生產的時間,都是沒有具體管制的。經過詹老師調整廠內生產的各細節後,材料加半成品庫存的周轉率從2014年的一年周轉60次,改善到2019年的一年周轉102次,相當於是每3.5天周轉一次。拉動成功推行後,也大幅降低了生產交付週期,從2014年的7~8天,降至2019年的5天,甚至3天也能夠趕出來,相較之下,我們的同行基本需要10~12天才能交付。
先拉動再暢流,重新定義製程
按詹老師教的的方法,在成功拉動後,我們後續透過持續的暢流改善,將整條線的效率從每小時出250台,提升到420台。此外,原先我們一台沖床每日換料約需停工160分鐘,在推動快速換料後,可降至每日僅停工20分鐘,換模時間也從原來的近120分鐘改善到40分鐘,將沖床稼動率從75%提升到92%。我們在穩固了精實生產拉動的原則後,在交付沒有問題,生產井井有序的前提下,透過線平衡的研究、快速換模的應用,以及TPM體系的搭建,不斷改善,甚至可以推行能源節約,達到每一年比前一年減少超過1000萬人民幣能耗的目標。
其實從前在壓縮機以外的工廠,也是有推動暢流的,但是做了之後沉澱不下來,因為在生產無序的狀態下,暢流改善產生的效益是遠比不上因產供銷銜接不暢造成的損失大。所以我才認為詹老師「先拉動,再暢流」的觀念至關重要,因為穩固了生產,才有可能真正維持暢流的效果,且穩固了自己廠內的生產後,我們還能將精實生產推廣到我們的供應商。
當年我們的精實生產成功之後,供應商就跟不上我們的節奏了,且從財務上的角度來說,集團也會要求供應商每年採購價格調降。但是對供應商來說,他若沒有降低成本的方法,很可能會虧損。因此我們學習最初豐田的做法,輔導供應商推動精實生產。我們向供應商投電子看板,推動他們JIT回貨,讓他們按照小時級,在固定時間給我們供貨。我們的倉庫都改建為車間,僅有車間周圍一點點面積是供物料暫存幾個小時的,空出來的空間又能夠用來增加產能。自2017至2019年,我們已經將精實生產推廣到42家核心供應商。
單靠5S足以實現智慧製造嗎?
2017年,我以集團專家的身份前往日本東芝電器考察。美芝的前身是東芝跟萬家樂合資建成的,之後萬家樂被美的收購,改名美芝,最初籌備美的壓縮機廠時,就有精實一條流(單件流)的思想,工序與工序之間的斷點較少。在我的想象中,東芝肯定有扎實的精實基礎,實際考核後,發現他們5S雖然做得好,但庫存量很高,且生產沒有用看板,生產計畫也沒有彈性,雖說品質管控嚴謹,但組織活力遠不如美的集團。沒有JIT、沒有自働化、沒有圍繞著經營持續改善,效益就不會好。
如今我已經離開美的兩年多,輔導過許多家企業推行精實生產,我認為,精實生產能否推動,與工廠規模大小,其實關係不大。拉動、TPM和快速換模,都是不花錢的。許多人誤以為要推動精實生產,就需要先將容器標準化,事實上是不用的,在拉動後,一定會讓庫存下降,在我輔導的企業中,甚至有推動精實後將多餘容器賣掉的。精實生產究竟能不能成功推動,我總結了三個重要的因素。
- 人的素質:學習精實生產的人,一定得有幾個明白人
- 執行力:沒有很强的執行力,是很難去推動精實生產的,因為推動過程中會遇到很多困難
- 考核文化與機制:在日常工作中有衡量員工績效的指標,也有一致的目標,去一同提升效益,推動過程也要有機制保障,讓大家既要有壓力也要有動力。此外,若規劃工廠時,就有一條流的概念在,也比較容易推動精實生產
詹老師的學識淵博,且無論教我們什麼,都是緊扣經營的。我們認識的詹老師的所有學員,都對詹老師非常敬佩,而老師能得到我們所有人的敬重,是因為他負責到底的態度、情懷與人格魅力。詹老師帶給我們正向的影響,教會了我們要懷著感恩的心,盡自己所能,為企業,為社會,做出貢獻。真得要做好還是很不容易的,但我們一直以老師為指路明燈,牽引著我們往對的方向前行。
延伸閱讀: