通過精實生產,企業可以實現資源的最大化利用,減少浪費,提高效率,並建立靈活且具回應性的生產體系。這不僅有助於維持企業的競爭優勢,還能夠促進環保與社會責任,確保企業在未來的市場中持續發展。通過引入和實施精實生產,二代接班人將能夠以可持續且創新的方式,繼承和發揚企業的優良傳統,帶領企業邁向新的高峰。
炬將科技是一家製造工具機外箱的板金工廠,成立20餘年來,追求熔接技術的提升不遺餘力。
林原正總經理,2006年時被迫提早接班,突如其來的任務讓他措手不及,才28歲的他,接班前在工廠負責設計與廠務,看到板金工廠傳統的運作模式,沒生意的時候沒事做,有生意卻做不來;接到大單時,人力與產能無法負荷,為應付訂單,毫無章法的生產方式,堆積大量庫存,工作現場堆滿半成品,且交期平均都在7周以上,這些都是同業的常態;而這些庫存於2008年,也因金融海嘯變成廢鐵。
林原正總經理,2006年時被迫提早接班,突如其來的任務讓他措手不及,才28歲的他,接班前在工廠負責設計與廠務,看到板金工廠傳統的運作模式,沒生意的時候沒事做,有生意卻做不來;接到大單時,人力與產能無法負荷,為應付訂單,毫無章法的生產方式,堆積大量庫存,工作現場堆滿半成品,且交期平均都在7周以上,這些都是同業的常態;而這些庫存於2008年,也因金融海嘯變成廢鐵。
「這也是為什麼,台灣大多數的板金工廠規模只能到一定程度。若要突破成長,就要解決現有的問題。」原正說道;同時這也是他接班後的一項大課題。
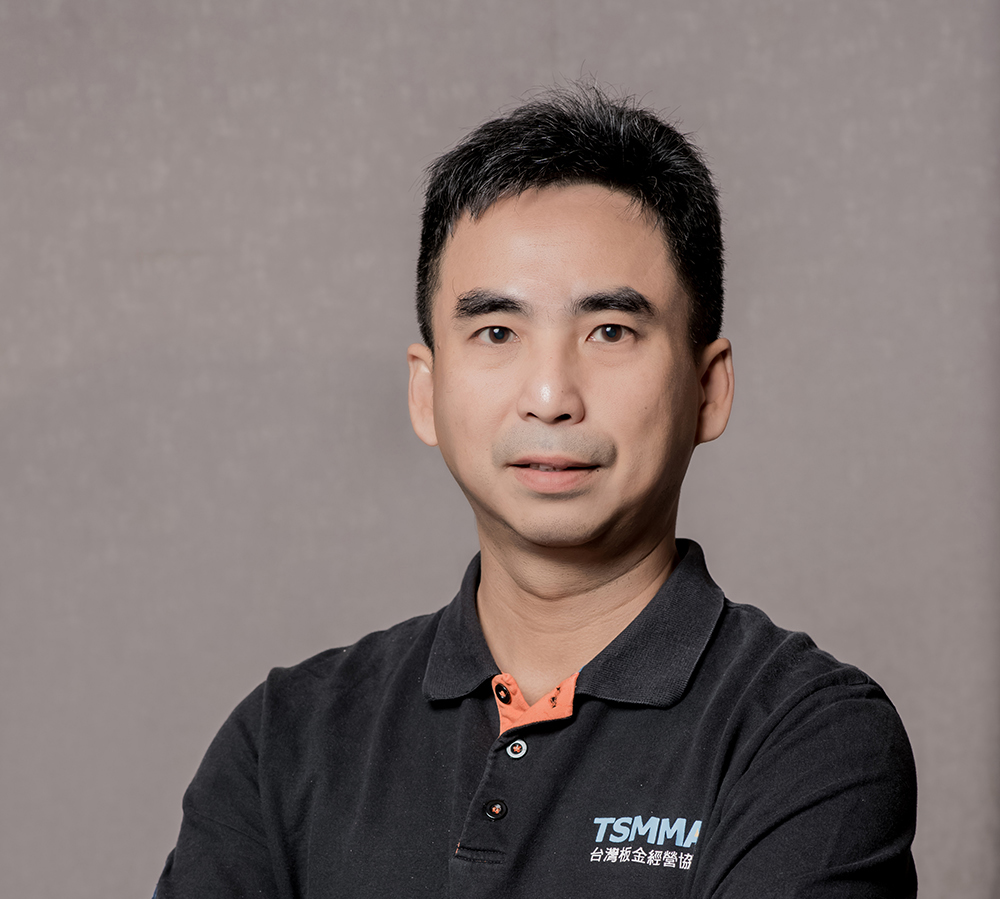
2006年時林原正總經理踏入詹志輝顧問的課程中,從策略地圖開始規劃公司整體經營方向,從中再導入六標準差、戰略業務銷售與精實生產…等系統工具。像炬將科技少量多樣,而且每一張訂單都有可能是唯一一次訂單。這類的工廠在全世界沒有人推動即時生產。「我把炬將精實生產的歷程分成三個階段」原正說道。
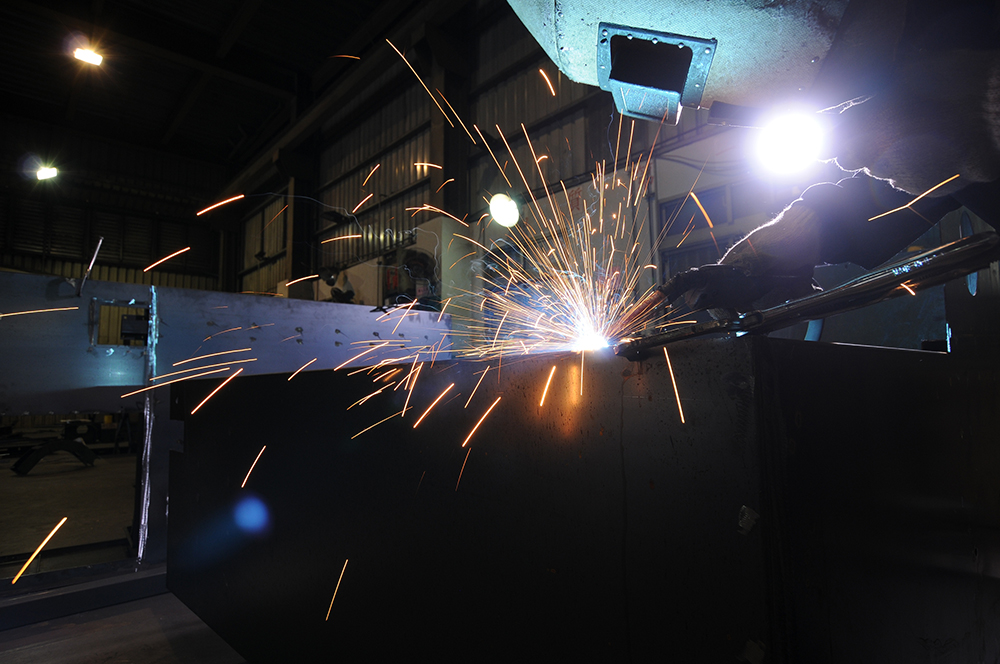
從WHOLE-PART-WHOLE拓展效益
- 第一階段:WHOLE-學習階段
當時完全沒有接觸過精實生產,所以向詹志輝顧問學習,從價值、價值流、推動與拉動及完善開始學。我們開始到客戶端訪談瞭解痛點,從中找出我方交貨的問題,客戶的訂單都是有組裝前後順序的,從訂單的組裝工序調整,分批出貨開始改善,和客戶一起找出最快組裝的最佳生產方式。從接到顧客訂單後先將訂單拆解後展成製令,將拆解的製令依序排在焊接工程,把焊接工程做為基準節拍點,然後從焊接工程發出看板(Kanban, 生產訊號卡),用焊接工程的需求拉動雷射切割和折床。如此一來,焊接產能會排滿,雷射切割和折床所有的工作都是為了焊接而做,不會有順序錯誤導致互相等待或過度生產的問題。效果顯著,修正後不到半年,交期從原本的45天瞬間縮短成21天。
- 第二階段 PART
為了更貼合客戶需求,原正開始思考細部調整,原先接拍點設置在焊接,但同時也限制產能。再與詹顧問討論過後,炬將把製程拆解得更細,與供應商訪談確認交貨日程,然後把節拍點從焊接移到折床,把產能發揮到最大。再次把交期從21一天再縮短至14天,工廠效率提升庫存大幅下降60%,客戶下訂單後拉動生產,完全不用承擔多生產的壓力,客戶端也不用再額外存放板金庫存。一年內有如此優秀的成績,與業界相比,要做到和炬將一樣的量,需要投入更多人力和設備,但炬將卻完全沒有增加設備和人力;炬將更和客戶共同舉辦聯合發表會,把這些年來的成果分享給板金同業學習。
- 第三階段 WHOLE
精實生產帶來最大的效益就是交期,炬將把第三階段重心放在資訊化,透過與東海大學AI團隊合作,把每個拆解的訂單運用數據精準算出製作週期,訂定排單規則,每個製程如何做連續流,再依照行業屬性計算接拍點。現在已經可以達成10天交貨含噴漆。原本是產業淡季的2月,炬將的訂單更是創了30年來的新高。可視化最佳生產方式後,炬將現在更著重在精度與品質改善問題。
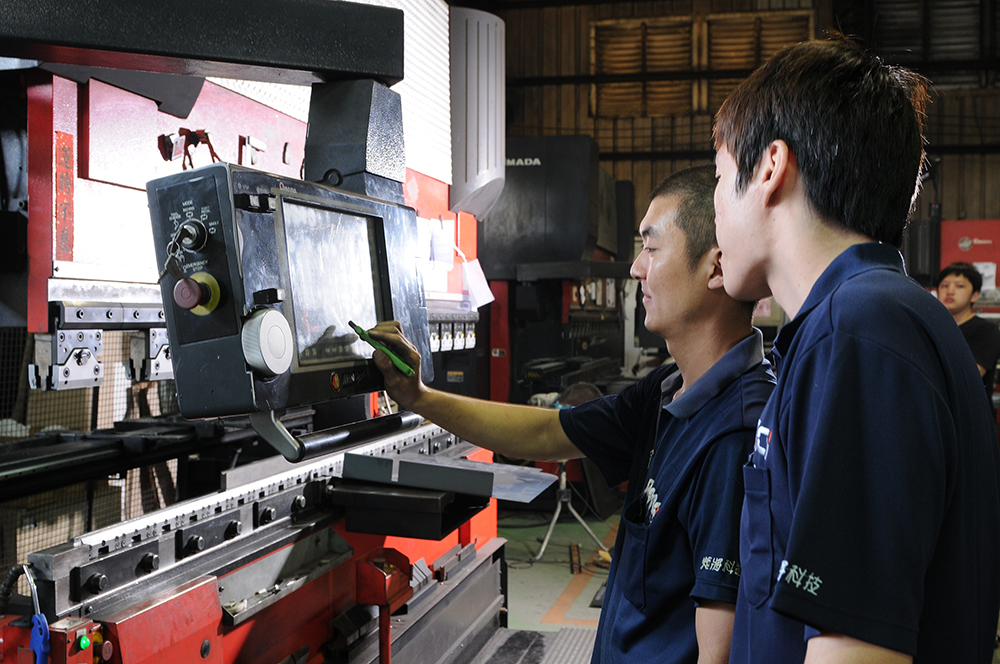
▲ 炬將科技工廠內部
成立板金協會,追求開放的板金加工文化
台灣大多數板金加工業都靠著自己摸索,腳踏實地的做工,但現在台灣的板金加工廠要面對的挑戰絕非台灣自己人,而是來自震盪不止、千變萬幻的全球市場。過去三四十年來辛苦經營的一代企業主,開始準備接手的二代接班人,都感受到市場需求不斷改變下產業的生態巨變,一個人關起門來、單打獨鬥的日子已不復返,接下來是跟著夥伴攜手合作的時候了。
台灣大多數板金加工業都靠著自己摸索,腳踏實地的做工,但現在台灣的板金加工廠要面對的挑戰絕非台灣自己人,而是來自震盪不止、千變萬幻的全球市場。過去三四十年來辛苦經營的一代企業主,開始準備接手的二代接班人,都感受到市場需求不斷改變下產業的生態巨變,一個人關起門來、單打獨鬥的日子已不復返,接下來是跟著夥伴攜手合作的時候了。
原正認為,唯有跟最了解板金業的對手,公開對話、交流切磋、互相督促,發展競合關係,才能開創出前所未見的板金加工格局。因此他將炬將多年的成果與同業分享,創辦台灣板金經營協會,他表示「全世界有板金製造的國家不多,如:德國、瑞士、日本、泰國…等,台灣競爭力絕對再前五名,很適合發展整體產業品牌。現在板金生態多數是拿著一張訂單到處比價,若能夠透過精實生產讓產業更具競爭力,就能共享共榮。」
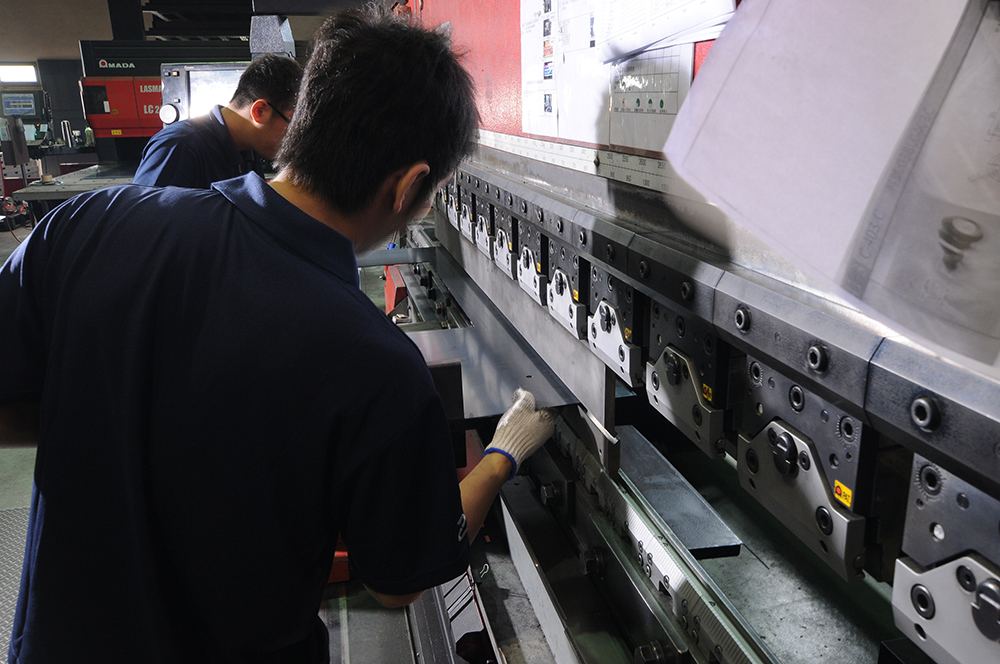
▲ 炬將科技工廠內部
接下來炬將會朝第四階段前進,更深化精實生產並與東海大學AI團隊共同研發軟體,實現資訊自働化、低成本智慧製造 (LCIM)。
接下來炬將會朝第四階段前進,更深化精實生產並與東海大學AI團隊共同研發軟體,實現資訊自働化、低成本智慧製造 (LCIM)。
延伸閱讀:六標準差:新代科技品質管理的突破點