在現代製造業中,低成本智慧製造(LCIM)正成為工廠提升競爭力的關鍵策略。通過結合先進的自動化技術和智能數據分析,LCIM實現了生產過程的優化與成本的顯著降低。這種創新方法不僅提高了生產效率和產品質量,還大幅度減少了浪費和資源消耗。對於工廠而言,LCIM的引入意味著更靈活的生產線、更迅速的市場反應能力以及更高的投資回報率。隨著全球製造業不斷向智能化和數字化轉型,LCIM正引領著工業革命的新潮流,為工廠的可持續發展和長期成功奠定堅實基礎。
試想一下,若工廠有十萬多副模具,每月約有六千張訂單,行銷全世界,你會怎麼管理工廠呢?
這不是個假設題,而是台灣最大的油封製造商茂順密封元件的工廠現況。多樣、少量的訂單,製程多、換線也多;茂順當時與其他製造業一樣,全是仰賴生管的個人經驗來管理現場,產線各站自行掌握排程,並用KPI管理交期,現場毫無章法。雖說若只是單純看結果,看是否能夠交貨,或許沒有問題;但若從生產過程來看,排程、交期、庫存、人力安排…等,問題多到無法掌握。因為孤島生產會產生大量線邊倉,不管交期好不好,工廠裡總是堆滿東西。
這不是個假設題,而是台灣最大的油封製造商茂順密封元件的工廠現況。多樣、少量的訂單,製程多、換線也多;茂順當時與其他製造業一樣,全是仰賴生管的個人經驗來管理現場,產線各站自行掌握排程,並用KPI管理交期,現場毫無章法。雖說若只是單純看結果,看是否能夠交貨,或許沒有問題;但若從生產過程來看,排程、交期、庫存、人力安排…等,問題多到無法掌握。因為孤島生產會產生大量線邊倉,不管交期好不好,工廠裡總是堆滿東西。
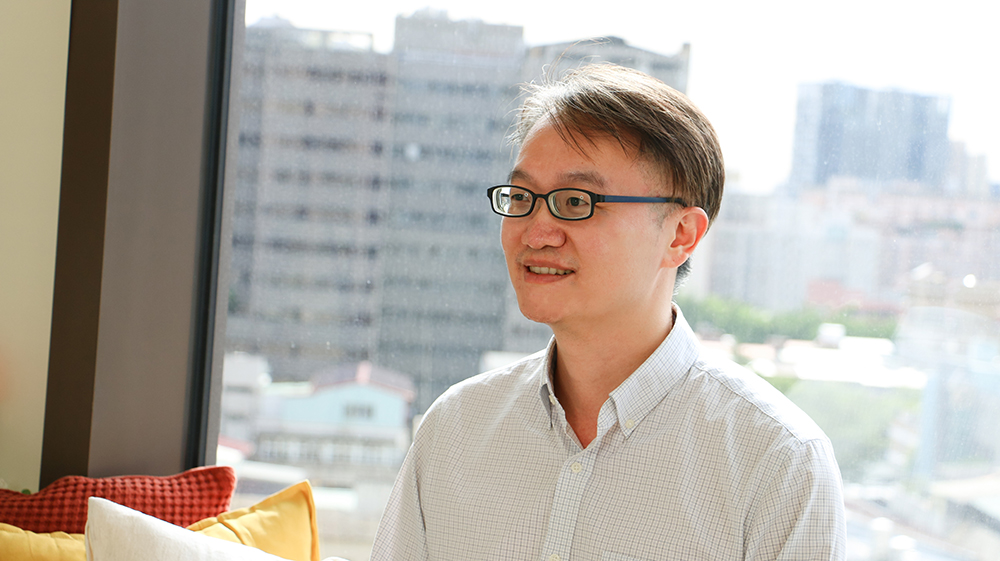
當時在現場擔任生管部經理的石銘賀說,「這樣沒問題嗎?若只是單純看是否有交貨,當然會沒問題。但若從排程、交期、庫存、人力安排…等,問題多到你無法掌握。因為孤島生產,會有一堆線邊倉,你永遠看不懂負荷,不管交期好不好都堆一堆東西。」
堆積的庫存拖垮效率
以往的做法,在每個製程前面放置線邊倉,現場將近700籃,每籃20~30公斤,主管再安排加工順序,換線也高達每天150筆,這些只是鐵殼製程,還不包含其他產線的半成品。這些半成品堆滿產線、倉庫,平均800坪的廠房一、二樓都是滿滿的線邊倉及半成品庫存。數量龐大,可想而知若找零件也需要耗費很長的時間。深入現場管理的石經理發現,所有的製造廠都會遇到相同的問題,他開始大量閱讀、找尋資料,想找到解決問題的答案。
石經理說,「當時真的很痛苦,明明知道問題出現在哪,但是苦於沒有解決的辦法,我在心中告訴自己,若一直用這樣的方法生產,茂順將止步於前。」所以茂順決定於2012年導入精實生產。
以往的做法,在每個製程前面放置線邊倉,現場將近700籃,每籃20~30公斤,主管再安排加工順序,換線也高達每天150筆,這些只是鐵殼製程,還不包含其他產線的半成品。這些半成品堆滿產線、倉庫,平均800坪的廠房一、二樓都是滿滿的線邊倉及半成品庫存。數量龐大,可想而知若找零件也需要耗費很長的時間。深入現場管理的石經理發現,所有的製造廠都會遇到相同的問題,他開始大量閱讀、找尋資料,想找到解決問題的答案。
石經理說,「當時真的很痛苦,明明知道問題出現在哪,但是苦於沒有解決的辦法,我在心中告訴自己,若一直用這樣的方法生產,茂順將止步於前。」所以茂順決定於2012年導入精實生產。
2013年,茂順決定導入精實生產。在詹志輝顧問的帶領之下,團隊同仁們學習運用精實生產拉動。先規劃價值流程圖,並決定基準節拍點,節拍點前以拉式生產,節拍點後以推式生產,並在下單時就決定排程。
理論看似簡單,卻讓我們在設計節拍點時吃足苦頭,就在眾人絞盡腦汁之際,詹老師提出了一個精妙的設計。由於過去生產過程的瓶頸點是「加硫」,便將基準節拍點設置在加硫前的三合一備料製程。精實拉動所帶來的全新觀念,很快就在工廠內部推展開來,並帶來極佳成效。過期的膠料數量從每月100筆降低為0筆──因為夏天膠料不會過期,得以現產現用,大幅降低了成本及不良率。工廠儲位減少70%,現場不再需要照看排程的人員,省去確認時間,也降低了管理壓力。
此外,之前因為組長不想浪費換線時間,大批量生產的庫存降低了50%,騰出的空間能給其他產線運用,產能增加10%。在沒有增加人力及費用的情況下,以最小資源達到最高產值,有效減少浪費。
在精實生產的道路上,石經理也逐漸改變思維邏輯,「這是完全不同的生產觀念,精實是引導我們做整體改善的思考,而非單點。雖然理論與現場實務總是衝突,中間也必須面臨到非常多的挑戰。但詹老師也告訴我,要把自己定位成一位價值流經理,而不是單純管製程的生管,才能從整個價值流程的角度,來進行全面的改善。」
▲ 茂順密封元件工廠
理論看似簡單,卻讓我們在設計節拍點時吃足苦頭,就在眾人絞盡腦汁之際,詹老師提出了一個精妙的設計。由於過去生產過程的瓶頸點是「加硫」,便將基準節拍點設置在加硫前的三合一備料製程。精實拉動所帶來的全新觀念,很快就在工廠內部推展開來,並帶來極佳成效。過期的膠料數量從每月100筆降低為0筆──因為夏天膠料不會過期,得以現產現用,大幅降低了成本及不良率。工廠儲位減少70%,現場不再需要照看排程的人員,省去確認時間,也降低了管理壓力。
此外,之前因為組長不想浪費換線時間,大批量生產的庫存降低了50%,騰出的空間能給其他產線運用,產能增加10%。在沒有增加人力及費用的情況下,以最小資源達到最高產值,有效減少浪費。
在精實生產的道路上,石經理也逐漸改變思維邏輯,「這是完全不同的生產觀念,精實是引導我們做整體改善的思考,而非單點。雖然理論與現場實務總是衝突,中間也必須面臨到非常多的挑戰。但詹老師也告訴我,要把自己定位成一位價值流經理,而不是單純管製程的生管,才能從整個價值流程的角度,來進行全面的改善。」
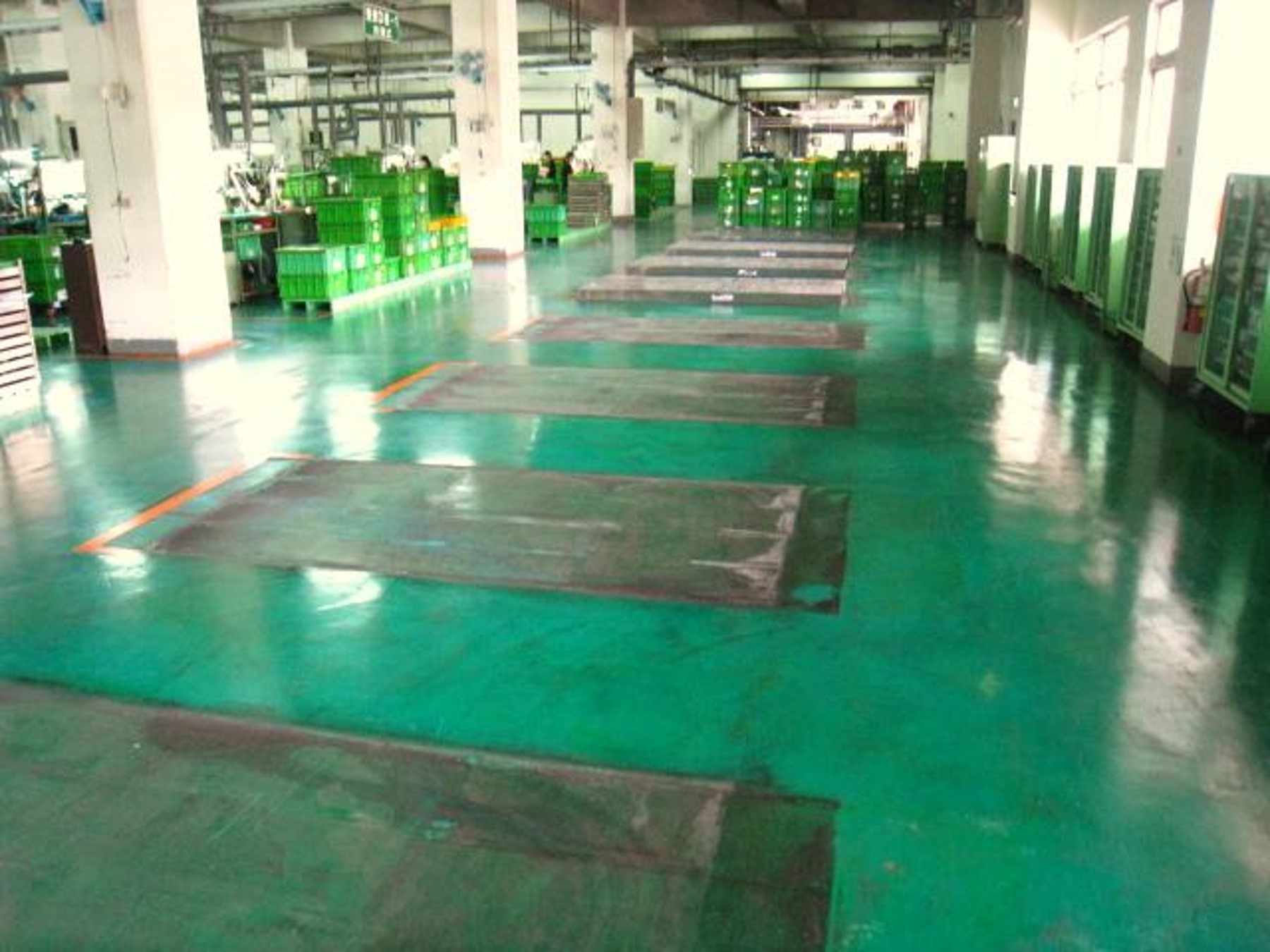
沒有精實生產的自動化,只是將城堡建構在散沙上。隨著精實生產觀念深根,我們的思維邏輯也逐漸轉變,發現這是與過去完全不同的生產觀念,精實是引導我們作整體的改善,而非只有單點。雖然理論與現場實務常常衝突,中間也必須面臨非常多的挑戰,但詹老師也告訴我們,要把自己定位成一位價值流經理,而不是單純管理製程的生管,才能從整個價值流程的角度,進行全面的改善。
從精實生產邁向自動化生產
多數製造業的目標都是實現自動化生產,縮短產品研發製作週期、降低成本、提高生產效率和產品品質,進而獲得整體效益。然而,橫在面前的最大阻礙是:工廠本身的條件是否符合自動化生產?
石經理表示,「運用精實生產把廠內製程精煉,整頓不必要的浪費,訂製規則與標準化作業,把產線資源發揮最佳,建立良好的基礎,著實降低成本,才能把自動化發揮到最好。所以我認為精實生產,才是實現低成本智慧製造(Low Cost Intelligent Manufacturing)的基石。」
茂順推行精實生產十年,現在已由機器手臂與無人搬運車取代人力,提升工作效率,從原本40人,降低70%以上。投入自動化設備最快2年就有機會回本,不管是一例一休還是環境安全…等,隨之帶來的是人力的管理與培訓成本的降低。近年茂順不受疫情的影響,成本依然穩定,維持售價不漲價,大幅提升市場占有率。
延伸閱讀:
多數製造業的目標都是實現自動化生產,縮短產品研發製作週期、降低成本、提高生產效率和產品品質,進而獲得整體效益。然而,橫在面前的最大阻礙是:工廠本身的條件是否符合自動化生產?
石經理表示,「運用精實生產把廠內製程精煉,整頓不必要的浪費,訂製規則與標準化作業,把產線資源發揮最佳,建立良好的基礎,著實降低成本,才能把自動化發揮到最好。所以我認為精實生產,才是實現低成本智慧製造(Low Cost Intelligent Manufacturing)的基石。」
茂順推行精實生產十年,現在已由機器手臂與無人搬運車取代人力,提升工作效率,從原本40人,降低70%以上。投入自動化設備最快2年就有機會回本,不管是一例一休還是環境安全…等,隨之帶來的是人力的管理與培訓成本的降低。近年茂順不受疫情的影響,成本依然穩定,維持售價不漲價,大幅提升市場占有率。
延伸閱讀: