精實生產是一種強大的策略,通過精細化管理和持續改進,不僅能顯著縮短交期,還能有效減少生產過程中的浪費並降低庫存水平。這種方法不僅提升了企業的運營效率,還在激烈的市場競爭中為企業贏得了更多的市場份額和客戶信任。
「計算結果告訴我們,66天的滾動WIP,就能支持這項生產活動,但生管人員卻準備90天的WIP,這多了近30天的庫存,也就是30天多餘的浪費」。
第一次接觸精實生產並畫出價值流圖後,本土企業的林益民總經理驚訝的發現,所謂的業界水準,根本就是大家一起向下沉淪比爛,既然他從父親身上接下這個重擔,他就要做到最好。最後,經過三個月的努力,庫存剩下37天,業界從此以他為標竿。
第一次接觸精實生產並畫出價值流圖後,本土企業的林益民總經理驚訝的發現,所謂的業界水準,根本就是大家一起向下沉淪比爛,既然他從父親身上接下這個重擔,他就要做到最好。最後,經過三個月的努力,庫存剩下37天,業界從此以他為標竿。
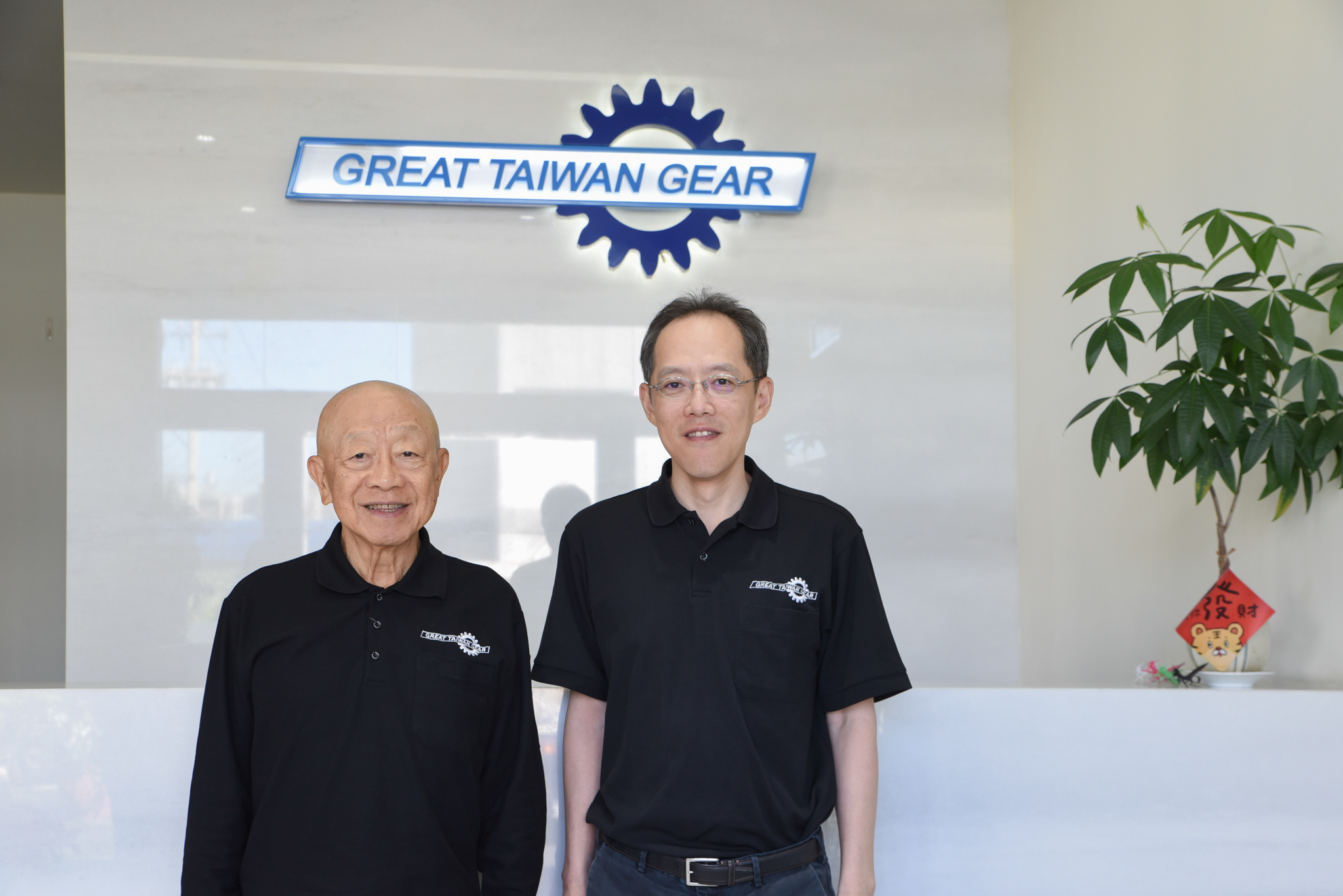
▲ 本土企業 林益民總經理
本土企業的90天精實生產傳奇歷程要從陳國課顧問開始說起…
本土企業的90天精實生產傳奇歷程要從陳國課顧問開始說起…
本土企業深耕新能源車齒輪高精密製造技術,除了是知名國際電動車廠齒輪供應商外,更透過培養系統整合研發能力,成功開發電動車單速齒輪箱,是國內第一家具備設計、生產、組裝電動車齒輪箱能力的供應商。
身為二代的總經理林益民接受我們的採訪,他說他一直保持終生學習的態度,不斷在外上課,透過知識找尋更多更好的方法,讓公司往正確方向成長。雖然公司在技術上擁有超強的競爭優勢,但在生產製造上,礙於原物料及製程,交貨期非常長。林總說:我們每個禮拜出貨至美國;公司以前是用ERP系統來排程,並不適用於現場管理,所以只能仰賴生管人員的經驗和方式來要求交期和庫存。
以精實生產大幅降低庫存的契機
還沒上課前,公司的D2D線上庫存為90天,林總自己也不知道這樣是否好或不好,心裡只覺得庫存可能有點高,詢問生管部門,給予的回應是,「這是業界的常態,沒什麼問題,應該不需要改變作法。」直到有機會認識陳國課顧問,陳顧問告訴他,現場這麼多庫存、交期這麼長,怎麼沒有想要學精實生產,並介紹詹志輝顧問的課程,請他帶團隊去上課;在那之前,林總及其團隊並沒有聽過或上過詹顧問的課,只覺得這個痛點一定要解決,於是林總親自帶了部門主管,報名上信瑞企管於2020年四月開的精實生產公開班。
「課程第一天老師就要我們繪製現況價值流圖,那次我上台去報告本土的現況價值流,詹老師開始問我很多製程的問題,我完全回答不出來,不是我對現場不熟,而是不知道這些數據跟管理工廠有什麼關係,這並不是我平時會去關注的地方。」林總回憶第一次上課情景,「原來精實的拉動式生產,與原先推動排單生產的方式有很大的不同;在最後一個連續流計算基礎節拍點,節拍點前拉,節拍點後推;這是精實拉動核心觀念。但這還是不是我最驚訝的地方,當我聽到原來庫存要放多少,是設計出來的,頓時我茅塞頓開;庫存有很多種型態,依不同的製程需求,去設計庫存,例如我們就很需要批量庫存,它是設計在兩個地方,例如我們需要高金額的材料備貨,或是半成品庫存,有了這些庫存設計方法,就不用耽心過度採購,或是生產太多半成品了。」
回去之後林總與本土團隊,從ERP系統拉出歷史資料,選取相對穩定的月份,從二十多個製程中,來看每個製程停留庫存的天數,找出改善方向,再把數據回填到價值流圖,很驚訝地發現整體的庫存只需要花費66天。
身為二代的總經理林益民接受我們的採訪,他說他一直保持終生學習的態度,不斷在外上課,透過知識找尋更多更好的方法,讓公司往正確方向成長。雖然公司在技術上擁有超強的競爭優勢,但在生產製造上,礙於原物料及製程,交貨期非常長。林總說:我們每個禮拜出貨至美國;公司以前是用ERP系統來排程,並不適用於現場管理,所以只能仰賴生管人員的經驗和方式來要求交期和庫存。
以精實生產大幅降低庫存的契機
還沒上課前,公司的D2D線上庫存為90天,林總自己也不知道這樣是否好或不好,心裡只覺得庫存可能有點高,詢問生管部門,給予的回應是,「這是業界的常態,沒什麼問題,應該不需要改變作法。」直到有機會認識陳國課顧問,陳顧問告訴他,現場這麼多庫存、交期這麼長,怎麼沒有想要學精實生產,並介紹詹志輝顧問的課程,請他帶團隊去上課;在那之前,林總及其團隊並沒有聽過或上過詹顧問的課,只覺得這個痛點一定要解決,於是林總親自帶了部門主管,報名上信瑞企管於2020年四月開的精實生產公開班。
「課程第一天老師就要我們繪製現況價值流圖,那次我上台去報告本土的現況價值流,詹老師開始問我很多製程的問題,我完全回答不出來,不是我對現場不熟,而是不知道這些數據跟管理工廠有什麼關係,這並不是我平時會去關注的地方。」林總回憶第一次上課情景,「原來精實的拉動式生產,與原先推動排單生產的方式有很大的不同;在最後一個連續流計算基礎節拍點,節拍點前拉,節拍點後推;這是精實拉動核心觀念。但這還是不是我最驚訝的地方,當我聽到原來庫存要放多少,是設計出來的,頓時我茅塞頓開;庫存有很多種型態,依不同的製程需求,去設計庫存,例如我們就很需要批量庫存,它是設計在兩個地方,例如我們需要高金額的材料備貨,或是半成品庫存,有了這些庫存設計方法,就不用耽心過度採購,或是生產太多半成品了。」
回去之後林總與本土團隊,從ERP系統拉出歷史資料,選取相對穩定的月份,從二十多個製程中,來看每個製程停留庫存的天數,找出改善方向,再把數據回填到價值流圖,很驚訝地發現整體的庫存只需要花費66天。
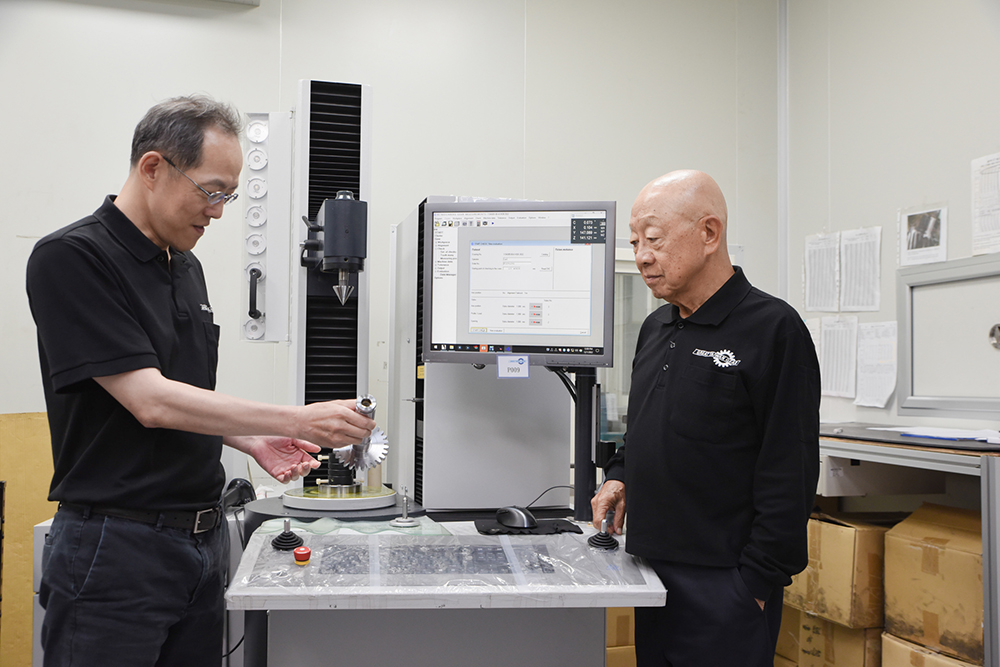
▲ 本土企業 林益民總經理
減少製程浪費,庫存成效彰顯
林總指出,「計算結果告訴我們,也就是66天的滾動WIP,就能支持這個生產活動,但我們的生管人員卻準備90天的WIP。表示現場將近有30天的庫存在等,這就是所謂多餘製造,產生沒必要的浪費。」觀念通了後,就剩下執行。內部開始做發量規則的變動;每週減量二天,共計15週。運用三個月的時間,成效顯著,庫存從90天降為60天、蝴蝶籠數量從900降到700,現場空出許多空間。
改變是困難的,員工都知道什麼是最佳的生產方式,但礙於現實面訂單常有突發狀況,會選擇較為輕鬆、減少換線的大批量生產方式,多製造庫存來因應。但精實生產推行後,員工知道這麼做他會變得更輕鬆、更有效率,不用因為訂單而加班生產,隨之也會跟緊自動調整。
達到階段性目標後,接下來是連續流的整併、上下製程整併,透過單元改善與庫存設計,在沒有增加人力的情況下,再度把庫存從60天下降至37天。精實生產只是開始,對於本土公司未來的發展,總經理林益民期許透過品質改善、技術研發…等系統工具,持續讓本土打造競爭力,以期成為業界的領導者。
林總指出,「計算結果告訴我們,也就是66天的滾動WIP,就能支持這個生產活動,但我們的生管人員卻準備90天的WIP。表示現場將近有30天的庫存在等,這就是所謂多餘製造,產生沒必要的浪費。」觀念通了後,就剩下執行。內部開始做發量規則的變動;每週減量二天,共計15週。運用三個月的時間,成效顯著,庫存從90天降為60天、蝴蝶籠數量從900降到700,現場空出許多空間。
改變是困難的,員工都知道什麼是最佳的生產方式,但礙於現實面訂單常有突發狀況,會選擇較為輕鬆、減少換線的大批量生產方式,多製造庫存來因應。但精實生產推行後,員工知道這麼做他會變得更輕鬆、更有效率,不用因為訂單而加班生產,隨之也會跟緊自動調整。
達到階段性目標後,接下來是連續流的整併、上下製程整併,透過單元改善與庫存設計,在沒有增加人力的情況下,再度把庫存從60天下降至37天。精實生產只是開始,對於本土公司未來的發展,總經理林益民期許透過品質改善、技術研發…等系統工具,持續讓本土打造競爭力,以期成為業界的領導者。