說到工業4.0大家肯定不陌生,2011年德國提出「工業4.0」以來,全球產業快速響應,龍頭企業也紛紛投入建置智慧工廠。然而,十多年過去,我們卻發現真正能完整實踐工業4.0 的案例並不多,尤其在中小企業中更顯稀有。這並非企業沒有投入,而是現實環境中存在三大導入困境:
- 導入成本高:智慧工廠涉及高度客製化與自動化設備,一旦需求變動,調整難度與代價極高。
- 系統架構複雜:工業4.0 通常需串接 ERP、APS、MES、WMS、IoT、機聯網等多套系統,光是建置期可能就長達數年,期間導致部門配合困難,系統彼此打架。
- 導入門檻過高:導入初期需要大量開發、建置與調校,加上人力短缺與技術斷層,使得多數中小企業根本無法起步。
一個經典案例是 adidas 在 2016 年於美國與德國設立 SpeedFactory,預計打造高度自動化且能快速供應在地市場的工廠。然而,短短三年內,兩座工廠皆宣告關閉。為什麼會如此?他們雖然表面上建構了自動化設備,但實際運作仍延續傳統的 MRP 排程邏輯,導致整體供應鏈無法與市場同步,既無法靈活應對需求變化,也無法有效控管成本與庫存,最終與預期效益落差甚大。
製造業的困境,並不只因關稅事件所導致
一、內部挑戰:成本太貴、交貨太慢、人力不足
許多製造業者持續投入資源,希望能在市場競爭中壓低成本、縮短交期。但實際上,我們經常看到一種矛盾的現象:企業越努力壓低成本,結果卻是成本越來越高;越想縮短交期,反而出現更多等待與瓶頸。問題常常出在方法的選擇。許多企業仍依賴過去的大量採購與大量生產邏輯,試圖透過以量制價與單位成本分攤來達成效益,這是典型的 MRP 系統思維。然而,在今日的市場需求已轉向少量多樣時,這種單點最佳化反而可能造成整體的浪費。
過度備料、過度生產導致庫存積壓,不只佔用倉儲空間,還可能干擾生產動線與物流效率;資金被綁在無法轉換為現金的庫存上,若產品或半成品具保存期限,更會產生報廢風險。這些現象都說明:若不從整體價值流重新設計流程,僅靠局部效率提升,是難以真正改善成本與交期問題的。
二、外部環境限制:關稅障礙、去台化壓力
即使沒有川普政府近期宣布的對中國商品提高關稅,台灣製造業早已面對外部環境的不利因素。這些制度性劣勢,導致我們在出口市場上的競爭力相對薄弱。更棘手的是,近年國際客戶因應地緣政治風險,開始擔憂台海局勢對供應鏈造成干擾,這使得「去台化」、「去中化」成為許多跨國企業重新設計供應鏈的主要策略。當客戶開始尋找替代產地,對台灣製造企業而言,這不只是訂單外移的風險,更是一場供應鏈信任的考驗。
三、顧客雙重要求:低價、少量多樣、快速交貨
客戶端對製造業的要求從未減輕,反而變得更加嚴苛。傳統上,「價格低」、「品質穩定」已是基本門檻,如今還加入了「客製化」、「少量多樣」、「交期短」等新條件。企業若仍以過往「壓低成本→大量生產→拉長交期」的模式來應對,勢必難以同時滿足所有條件。事實上,很多企業確實做到了交期變短、產品多樣,但卻發現毛利持續下滑,甚至在達成目標的過程中產生更高的隱性成本。這再次說明,若方法錯誤,再努力也是枉然。
這些頂尖企業正在這麼做
在進入技術與方法論的探討之前,我們先分享幾個與我們長期合作的企業案例,這些企業正是透過低成本智慧製造,成功應對內外挑戰並實現成長的代表。
1. 美的集團:從中國走向全球的製造韌性
中國美的集團,目前是全球最大的白色家電製造商,自2014年3月起導入低成本智慧製造,展開壓縮機工廠的改善專案。導入前的庫存周轉率為每年約 60 次,經過流程與生產模式的優化,去年已提升至 240 次;交期也從最短 8 天縮短至 3 天,遠優於競爭對手 10 至 12 天的交貨水準。
每條產線的產能,亦由每小時 250 台提升至 420 台,直接帶動集團整體營收顯著成長。美的並非僅限於中國市場,其全球製造布局已擴展至美國、德國與義大利,更收購了日本東芝(Toshiba)家電部門與其製造資源,堪稱全球製造在地化的經典案例。
2. 勤誠興業:人力精簡與效率翻倍的台灣代表
台灣伺服器外殼領導廠商勤誠興業,自 2021 年起在嘉義新廠全面導入低成本智慧製造。該廠僅以約 1/3 的人力,即可達到中國大型廠區上千人力的產能規模 。隨著內部成本結構的優化與效率提升,勤誠的業務拓展也隨之加速,營收自原本的 93 億新台幣,成長至去年的 145 億。此外,勤誠預計於今年年中完成其美國新廠的建設與量產,進一步實現就近供應的全球佈局。
3. 茂順密封:解決庫存問題、穩定提升營運績效
位於南投的茂順密封,是我們長期合作的企業夥伴。早期面臨在製品過多與庫存過期報廢的問題,導入低成本智慧製造後,成功大幅降低在製品庫存,並徹底根除庫存過期的風險,提升整體供應鏈的穩定性與資金周轉效率。
值得一提的是,我們輔導的多家企業,在解決庫存與效率等內部問題後,皆出現營運數據的明顯改善,甚至反映在股價上的穩定與上揚,形成良性循環。
4. 華泰鞋業:空間、效率與利潤的三贏局面
來自越南的華泰鞋業,導入低成本智慧製造後,不僅成功降低整體庫存水位,還釋放出大量廠內空間。整體製造成本明顯下降,進而提高了企業的毛利率與市場競爭力。前面提到的例子是想讓大家知道,低成本智慧製造並不像工業4.0那樣昂貴或複雜,無論是大企業還是中小型公司,都能輕鬆導入這套系統。接下來,將介紹這套系統的五大關鍵。
從LCIM到全球製造在地化的五大關鍵
一、低成本的價值流:先看清流程,才談改善
我們常說「低成本智慧製造」的第一步,不是買系統、不是上軟體,而是先做到一件事:用最簡單的方式,搞清楚你現在的流程發生了什麼事。所以我們的方法,是先從低成本的價值流開始,最重要的一步就是——畫出「價值流」。
1. 什麼是價值流?
簡單說,就是從客戶下單開始,一直到業務接單、採購、供應商交貨、生產、出貨、運送給客戶,全流程一站一站畫出來。畫的目的不是讓它變得複雜,而是要釐清:「哪些工作真的有價值,哪些只是浪費?」有價值的工作,是有助於提升產品品質、縮短交期;沒價值的工作,像是過多的庫存管理、重複搬運、報廢處理,就是浪費。
我們在輔導的時候,第一步就會請企業自己畫價值流,結果常常發現大家對自己流程的狀況,其實根本不清楚。所以,畫價值流的真正目的,是為了釐清三件事:
- 資訊是不是照對的順序流動?
- 物料是不是照對的時間送到?
- 每一站拿到的,是不是正確數量?
我們所說的「資訊管理」:不是一堆表單或系統,而是用最低成本、最簡單的方式,讓你重新看見流程中真正的問題在哪裡,確保各種資訊跟物件,以對的順序、數量跟時間送到對的地點。
低成本智慧製造的核心概念:JIT(Just In Time)及時生產,又叫拉動式生產,它跟傳統的 MRP(物料需求規劃)排程方式完全相反。傳統的 MRP 是怎麼做的?系統會把很多訂單合併起來,統一下單到最前面的製程。前段開始大量生產,一層一層「推」到後段。優點是可以大量採購、批量生產,減少換線換模的次數,降低單位成本。但這個方式有兩個致命問題:它假設市場是穩定、大量、標準化的。一旦遇到現在這種少量多樣、需求變動快的情況,就會造成大量庫存、等待與浪費。所以,我們要改用 JIT 的方式排產。
JIT 的核心很簡單一句話:「在剛剛好的時間,送來剛剛好數量的零件,到剛剛好的位置。」不提早、不過量、不積壓——這才是智慧生產該有的節奏。但 JIT 不是喊口號,它有一套具體做法。
第一步,還是要畫出價值流。接著,設定一個叫做基準節拍點的位置。這個點通常設在最後一個連續流程的起點,實務上,大多數的工廠會設在組裝線上。一旦有訂單進來,工單就「落在」這個節拍點上,然後這個節拍點就開始反向向上游喊話:我要什麼?要幾個?什麼時候送到?這就像是後段在「拉」前段配合生產,不是前面一股腦地做,而是後面要了才做,這就是「拉動式生產」的由來。這種節奏,一開始大家會覺得沒安全感,會擔心:「這樣會不會斷料?會不會來不及?」但只要把價值流、節拍點、需求溝通機制設計好,你就會發現,原來「不囤貨也能穩交期」,還能大幅減少浪費與存貨壓力。
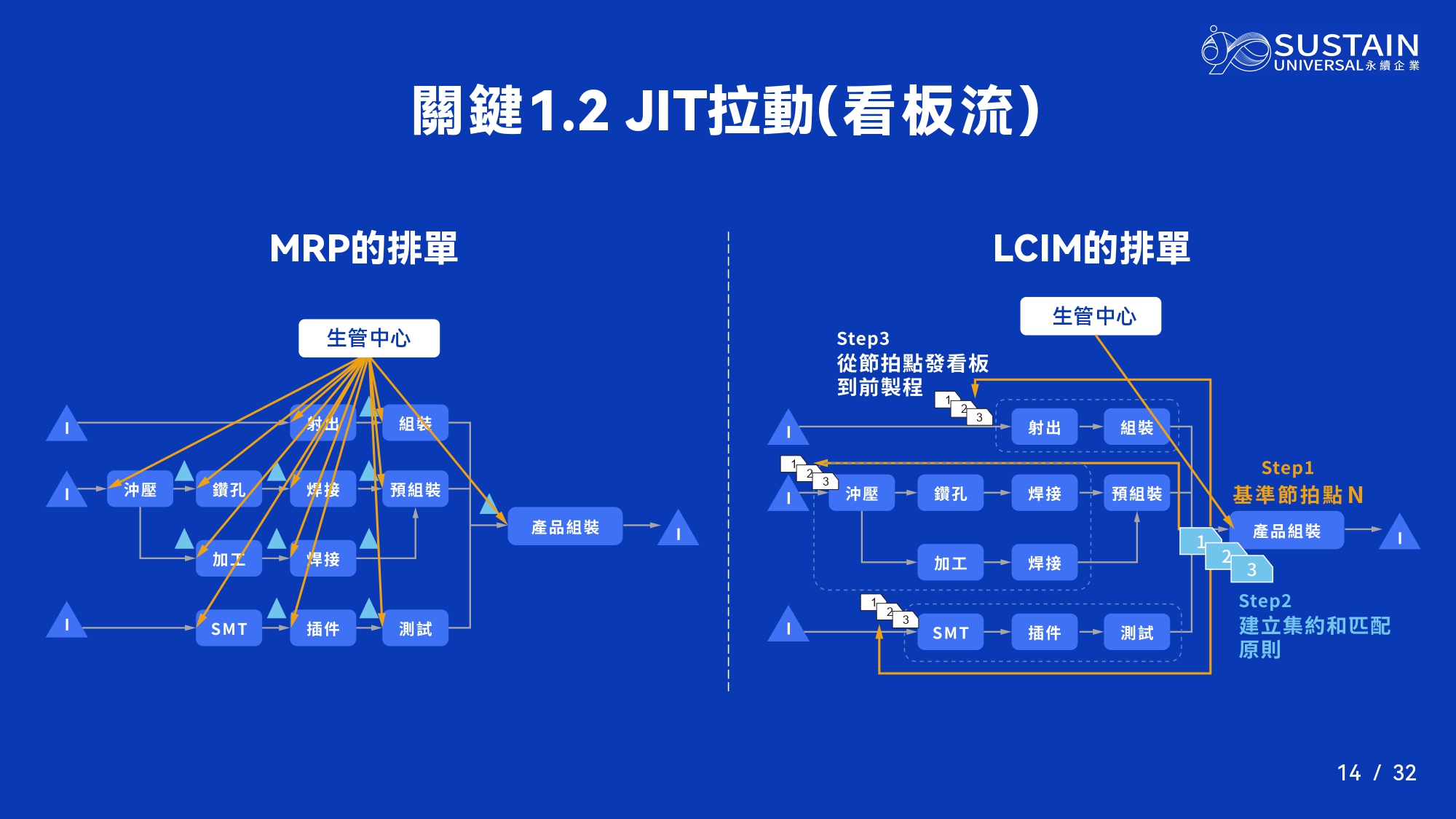
2. 看板的用處為何?
在拉動式生產系統裡,有一個非常關鍵的工具,叫做「看板」。它就像是生產線上的「指令卡」,負責在基準節拍點跟各個前段製程之間傳遞需求資訊。你可能會覺得,看板聽起來跟我們平常用的工單好像差不多?其實不一樣。看板是為了拉動式生產而設計的,有幾個很重要的規則:
- 沒有看板就不能生產:因為沒有看板,就代表沒有後段需求。你如果還硬生產,就是在做「沒人要的東西」,那只會變成庫存、浪費。
- 訂單不能合併生產:MRP 系統會為了效率把多個訂單合併一起生產,但在 JIT 裡不可以。每一張看板,就是一張訂單,也是一張工單——一對一對應。
那看板上會寫些什麼呢?
- 訂單編號(=工單編號)
- 看板的類型(是生產用?搬運用?補料用?)
- 預計和實際的投產時間與完成時間
這些資訊看起來很細,但目的只有一個:追差異、抓問題去做改善,讓整個拉動式生產系統越來越準、越來越穩。看板不不只告訴你「要做什麼」,還讓你有辦法知道「有沒有準時」、「哪裡出問題」、「要怎麼改善」。
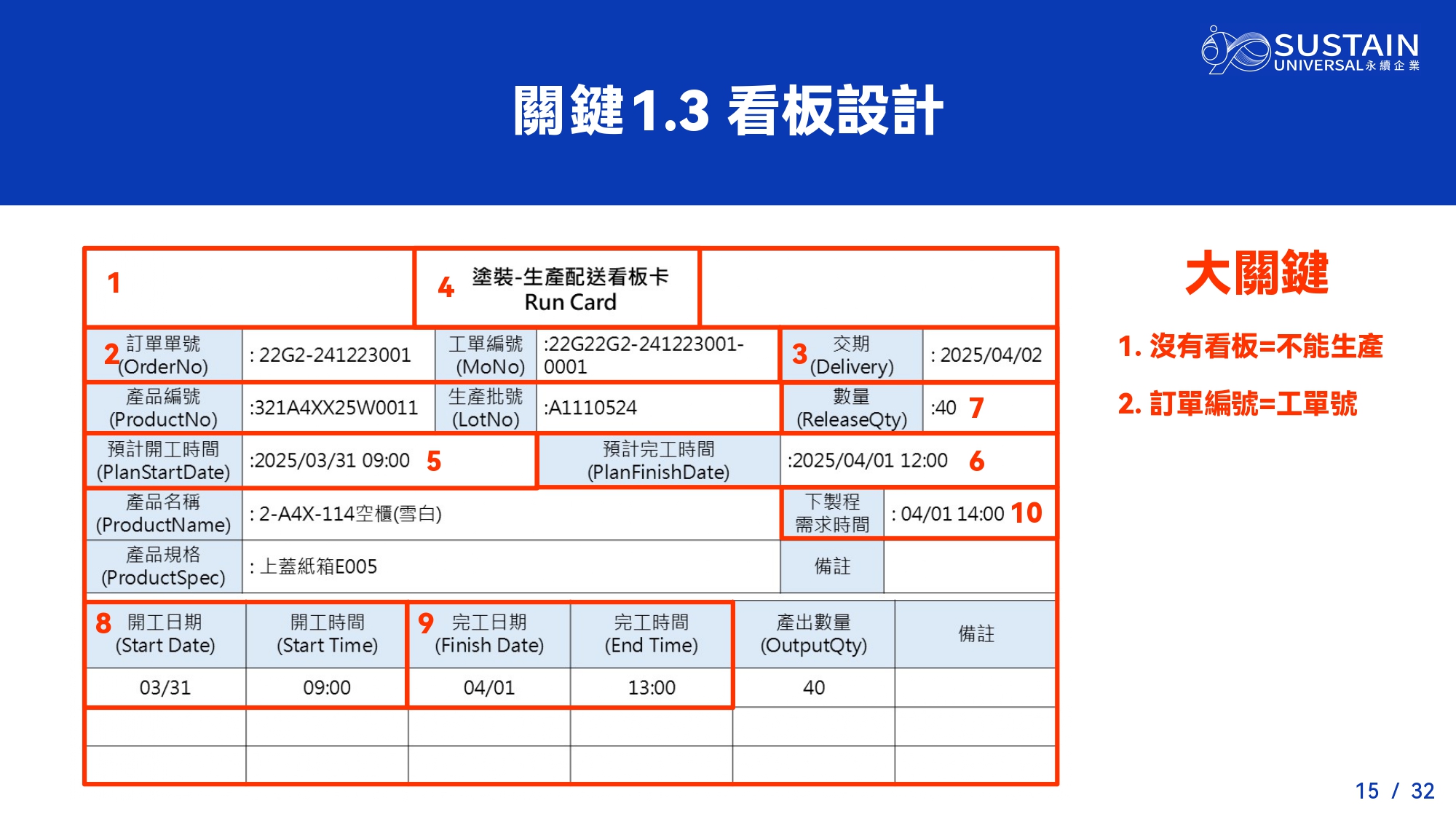
3. 設定精實KPI
當這整套拉動式生產系統跑起來後,就可以開始設 KPI 了。目標很明確,就是三件事:
- 成本有沒有降下來?
- 庫存有沒有變少?
- 交期有沒有變快?
這三個指標,就是低成本智慧製造的成效驗證標準。如果沒有達到,那代表一定有哪個環節還可以優化。可能是節拍點設錯了,可能是看板傳遞不準,也有可能是現場執行沒跟上流程。我們這一套方法,其實已協助數間工廠導入、落地過了,從機械業、電子業到食品加工都有。效果都很明顯,只要企業願意照著方法做,一定做得起來。
4. 搭配LEAN+APS先進排程軟體
從十幾年前開始在企業裡推動這整套工具。那時候還沒有什麼軟體可以搭配,就是用 Excel 排單、用手動報工的方式,一樣成功導入低成本智慧製造,幫企業提升了競爭力。所以才說,這是一種低成本的資訊管理。
它的邏輯很清楚、觀念也很簡單,不需要從頭寫一套超複雜的系統。這幾年我們也跟軟體公司合作,把整套拉動式生產的邏輯寫進去做成 APS 系統,讓推動起來更順、更省人力,也能進一步再降低成本。所以你會發現,這不是花大錢才能導入的智慧製造,而是人人做得起的「低成本智慧製造」。
5. 經典案例——美的壓縮機的生產流程
紅色的是最終的組裝線(AC),下面這四條藍色線,就是壓縮機必備的四個零組件的生產線。你會發現一個有趣的現象:總裝是在 7/2 上午 10 點開始,但這些零件,幾個小時前才剛開始製造。甚至有些工段的時間是重疊的,也就是說,他們是一邊生產零件,一邊往總裝線送,零件做出來馬上就用,根本沒有時間變成庫存。靠這種方式,美的把原本 8 天的交期,縮到最快只要 3 天!
現場常有這種心情:「東西還沒準備好就開始生產?這樣會不會很危險?」所以很多工廠會怎麼做?所有零件都先做好放個兩三天,等確定萬事俱備才開始動工,或是某些零件提前一週就備好了,在現場等其他配件跟上。這些「等一等」的時間,加起來其實就是浪費。這些就是我們要挑戰、要打破的傳統思維。
二、先物流,再製造
我們在輔導過程中發現,很多公司在設廠的時候,一開始沒有先把物流動線規劃清楚,結果一開工就發現問題一堆——供應商進料、AGV自動搬運車、出貨碼頭、生產線全部擠在一起,互相干擾、效率低落。所以我們一直強調,規劃廠房的時候,一定要先確認好物流動線,再來設計產線。這樣才能做到「物流順,製造才順」。
前面我們提過,低成本智慧製造的核心之一就是「降低庫存」。當庫存降低,倉儲空間就可以縮小,廠內動線也不會因為堆滿原物料或半成品而擁擠,物流自然就順暢了。其實,光是庫存的種類就有九種:像是原物料跟零件的超市庫存、因應最小訂購量(MOQ)產生的批量庫存、調節淡旺季差異的調節庫存等等。
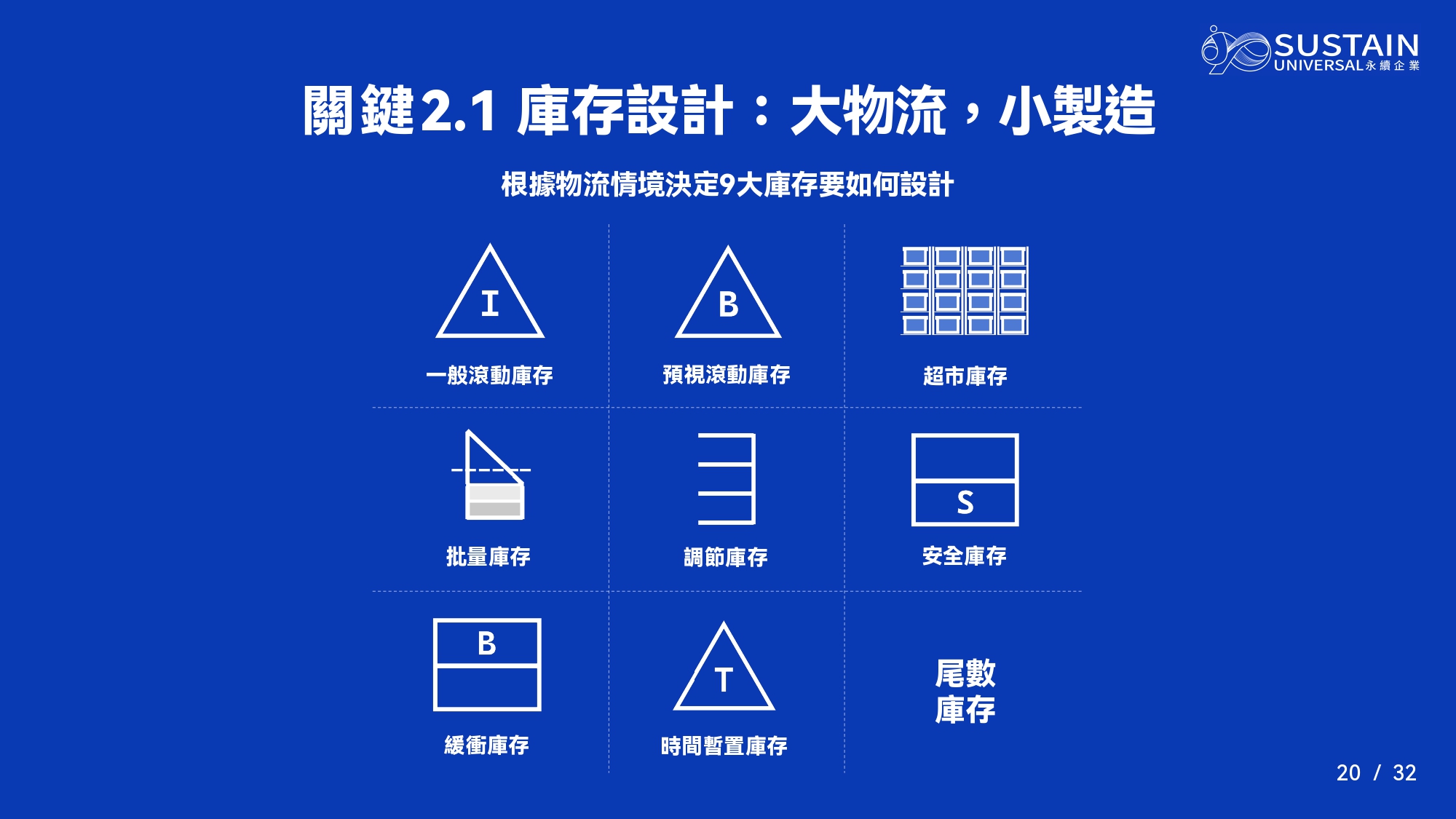
那供應商管理怎麼做?我們的做法是這樣:當某項物料快不夠的時候,系統會自動產生看板,直接通知採購補料。不需要再反覆確認、打電話催料,這些都交給系統依照規則自動執行。簡單、明確、效率高,也符合「低成本智慧製造」的精神。
三、零人設計
指的是在規劃產線時,一開始就用「完全自動化」的方式去思考設計。為什麼這麼做?因為設備跟機器手臂不像人一樣可以靈活移動,它們體積大、佔地多、改動成本高。如果一開始是用人力導向的方式設計產線,等到後續要導入自動化設備時,常常就會卡在空間不夠、動線打架、整條線要重改,不只耗時還耗錢。因此,用此邏輯來設計產線,即便一開始還沒導入所有設備,至少空間、流程都已經預留好,未來升級才不會卡關。
現在的自動化設備成本已經大幅下降,機器手臂已經不是高不可攀的投資,而人力問題卻越來越嚴重,找不到人、訓練成本高,這些都是企業天天在面對的痛點,因此早點佈局,便能早點享受到自動化帶來的穩定與效益。在自動化尚未完成的階段,我們需要進行生產線的單元設計。常見的設計方式有:
- U型線:適合工人協作,也便於管理監督。
- 豆莢型線:讓一個工人執行多個工序,提升效率。
- 組合型產線:綜合不同產線的優點,提供更多靈活性。
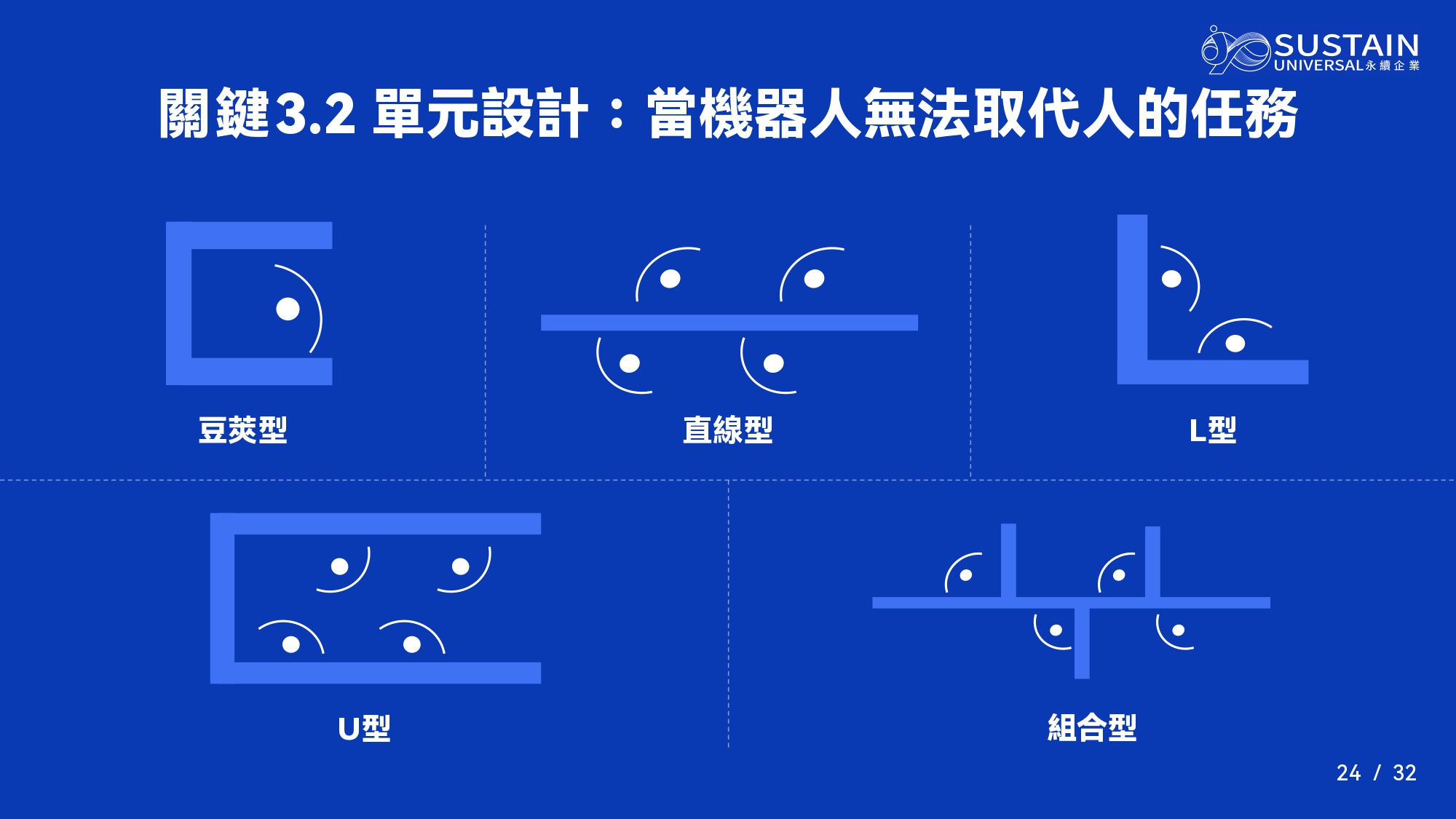
零人設計的核心概念是: 在規劃設廠時,預留空間給自動化設備,等到需要人力時,再根據情況進行調整。這樣從零人設計到導入人力,再到自動化,整個過程更順暢。完成前面三個步驟後,就可以開始規劃建築設計了。這時,內部物流動線、產線規劃等都已經確定,接下來要處理的是外部建設,這是一個由內而外的過程。我們輔導的企業有時會使用樂高來模擬內部動線和布局,建議大家也可以這樣做。
最後,前面四個步驟在台灣經過POC驗證,確認可行後,所有環節都已經無礙,這樣在全球擴廠時就能夠快速落地。我們推動低成本智慧製造已經十幾年,從最初的理念與企業輔導工具,到如今與曾經輔導過的企業組成聯盟。我們與江氏集團冠理科技合作,利用拉動式生產概念開發APS軟體,與專門製作機械手臂和控制器的新代科技合作,還有被美的集團併購的德國庫卡,提供自動化與AI設備。從根本方法到軟硬體設備,全方位解決企業需求!
今天我們談到了低成本智慧製造如何從根本上重塑企業的生產方式,並證明了這套方法不僅在台灣得到了成功的驗證,還能夠快速地推向全球。要建設新工廠,首先要做的就是先導入LCIM(低成本智慧製造),這不僅是技術的應用,更是思維方式的根本改變。我們不只是跟隨工業4.0的腳步,我們已經打敗了工業4.0。因為我們所用的方法,已超越了目前的主流,我們也致力協助企業在全球競爭中脫穎而出。
如果各位在經營中遇到類似的困擾,我們誠摯邀請您。我們將深入提供企業健康檢查服務,從策略層面協助您明確定位改革的重點。在確定了最迫切需要改進的問題後,我們的專業輔導團隊會在短期內提供幫助您迅速解決當前的挑戰,在1年內達到財務見效,並協助強化接班團隊。